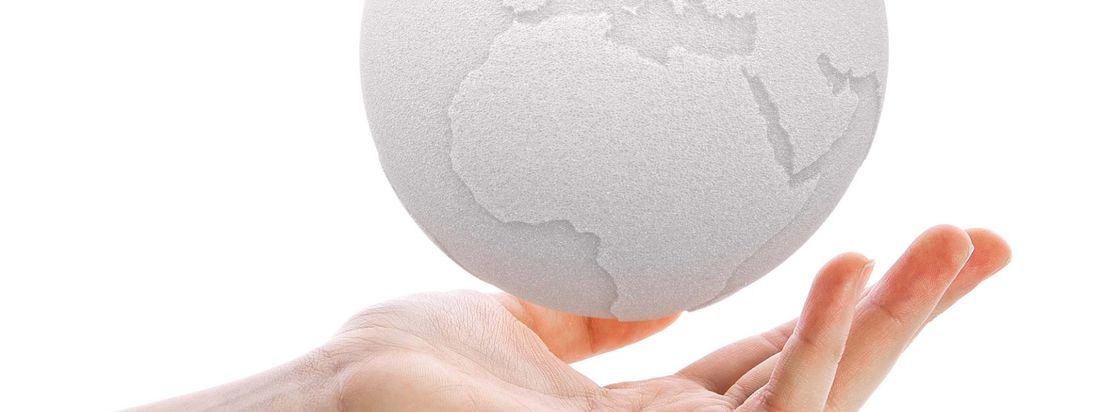
Foams for all your applications and processes
Whether your selection criteria include density, processing temperature, cell size or a specific mechanical property performance level, we offer a full line of structural foam products to meet whatever your project requires. ... MORE